The Plan-Do-Check-Act (PDCA) cycle stands as a cornerstone methodology. It’s a simple yet powerful tool for driving continuous improvement, fostering a culture of learning, and achieving organizational goals.
Understanding the PDCA Cycle
The PDCA cycle, also known as the Deming cycle or Shewhart cycle, is an iterative four-step approach that involves:
- Plan: Identify a problem or opportunity for improvement, establish clear objectives, and develop a plan to address the issue.
- Do: Implement the plan on a small scale, testing the proposed solution in a controlled setting.
- Check: Evaluate the results of the implementation, gathering data and analyzing the outcomes to assess the effectiveness of the solution.
- Act: Based on the evaluation, standardize the new process or make adjustments as needed. If the solution is successful, incorporate it into the standard operating procedures. If not, repeat the cycle with a revised plan.
The PDCA cycle is not a linear process; it’s an ongoing cycle of improvement. As organizations apply the PDCA cycle repeatedly, they gain a deeper understanding of their processes, identify areas for further improvement, and continuously enhance their overall performance.
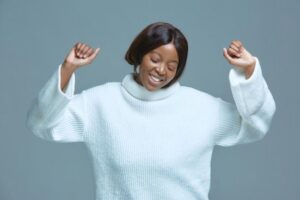
Real-world Examples of PDCA in Action
To illustrate the practical application of the PDCA cycle, consider these examples:
Example 1: Reducing Customer Complaints
A company experiencing a rise in customer complaints about product quality initiates a PDCA cycle to address the issue.
Plan: Analyze customer feedback to identify specific product defects and develop a plan to improve manufacturing processes.
Do: Implement the plan in a pilot production line, introducing stricter quality control measures and enhanced training for production staff.
Check: Monitor product quality data from the pilot line, comparing it to previous levels to assess the effectiveness of the improvement efforts.
Act: If the pilot line demonstrates significant improvement, standardize the new procedures across all production lines. If not, identify areas for further refinement and repeat the cycle.
Example 2: Streamlining Order Processing
An e-commerce company seeking to reduce order processing times implements a PDCA cycle to optimize its fulfillment process.
Plan: Map out the current order processing workflow, identifying bottlenecks and potential areas for automation.
Do: Implement a new order management system with automated tasks, such as order validation and inventory checks.
Check: Track order processing times, comparing them to historical data to measure the impact of the new system.
Act: If the new system significantly reduces processing times, standardize its use across the organization. If not, identify areas for system refinement and repeat the cycle.
The Power of the PDCA Cycle
The PDCA cycle offers numerous benefits, making it a valuable tool for any organization seeking continuous improvement:
- Promotes a data-driven approach to decision-making: By emphasizing data collection and analysis, the PDCA cycle encourages evidence-based decisions.
- Fosters a culture of learning and experimentation: The iterative nature of the PDCA cycle encourages continuous learning and experimentation, leading to a more adaptable and innovative organization.
- Drives continuous improvement: By regularly evaluating and refining processes, organizations can achieve incremental improvements over time, leading to significant gains in efficiency and effectiveness.
Conclusion
The Plan-Do-Check-Act cycle is a simple yet powerful tool that can be applied to a wide range of business challenges. By embracing the PDCA cycle, organizations can embark on a journey of continuous improvement, enhancing their processes, products, and overall performance.